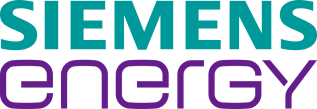
Tyne Pressure Testing performed hyperbaric ingress testing on a set of harnesses designed for a subsea environment within the oil and gas industry.
Read case studyCall us on +44 (0) 191 209 7490 to speak to one of our experts.
Hyperbaric testing is used to extensively test components that are required to operate at pressure levels higher than atmospheric conditions. This type of testing is performed on components used in offshore or subsea environments, as well as in extreme high pressure applications to test and verify that a product can operate under extreme, pressurised conditions.
We provide specialist hyperbaric testing services to a range of sectors across the globe. Housing nine hyperbaric chambers, including one of the largest commercial chambers in the world.
Chamber TPT 5, our largest hyperbaric chamber, has the capability to pressure test down to 4,500 metres, equivalent to 6,526 psi/450 Bar whilst simultaneously testing at temperatures down to -2°C. Automated controls and an interactive loading table support greater efficiencies with an ability to load, fill and fully pressurise in under 90 minutes. This chamber also benefits from being fully automated meaning any natural fluctuations in the likes of pressures and temperatures are self-regulated without the need for manual overriding. Automated controls are also used to simulate the movement of components within pressurised environments.
Our highly skilled and knowledgeable test engineers, who have over 20 years’ experience, are experts in hyperbaric testing and associated pressure testing services. Clients have the opportunity to draw on their specialist knowledge with the option to select our beginning to end, fully project managed testing service. Independent hire of the hyperbaric chambers is also available.
Did you know that we can facilitate remote viewing for hyperbaric testing? This encompasses live workshop footage and data streams to enable you to witness testing programmes and monitor product performance from any location worldwide. We can even record footage for review at a later date.
If hyperbaric testing is something that you are interested in, please contact one of our experts to discuss your requirements.
Our facility offers nine hyperbaric testing chambers ranging in size and pressure capability including the world’s largest, commercially available hyperbaric chamber which can simulate water depths down to 4,500 metres.
Explore the chambersHyperbaric testing is the application of external pressure to a component and is carried out in a specialist hyperbaric chamber to simulate extreme pressure environments. The component may be retained inside of the hyperbaric chamber by its own weight where heavy industrial products are concerned.
Retaining straps are used to hold buoyancy modules in place, or racking where separation is required for fragile components. Bespoke tooling can also be manufactured for specialist items.
Products are placed in hyperbaric chambers, which are often cylindrical in shape, before water is injected and then pressurised using pumps.
For every 10 metres below sea level, a water pressure of 1 bar is exerted. So, if a product was going to be deployed at 1,000 metres below sea level, the weight of the pressure on that product would be 100 bar.
High pressure instrumentation and pumping systems, rated over and above the maximum pressure of each individual chamber, are used to feed inhibited water into each chamber from on-site storage tanks. This water creates the desired pressure inside of the chamber.
Hyperbaric testing concerns the application of external pressure to a product. The product is housed within a pressure vessel/chamber which acts as the barrier to retain the external pressure around the test subject.
The primary reason for doing this is to replicate actual conditions an assembly will see in installed life, meaning the external pressure will first and foremost validate the structural integrity of the component. Secondary to that, any ingress of pressure into the component would highlight a leak path(s) which may compromise areas such as sealing arrangements or welded joints.
The principle of hydrostatic testing is very similar to hyperbaric testing in that this will also verify structural integrity and any leak paths, as well as utilising water as the test medium. The fundamental difference is that a hydrostatic test concerns the internal pressurisation of a component, rather than subjecting it to external pressure. The likes of a product sealing arrangement will still very much but scrutinised but with pressure effectively pushing ‘in-to-out’ rather than ‘out-to-in’.
Certain components may be subjected to a hydrostatic and hyperbaric test simultaneously e.g. subsea pipeline equipment. These products would typically feature primary, secondary and tertiary sealing barriers to withstand excessive levels of internal and external pressure.
Opt for either an all-encompassing, fully project managed testing service provided by our experts and in-house engineering team, or, hire our pressure testing facilities to conduct independent testing.
Our clients travel across the globe to utilise our pressure testing services and hyperbaric testing equipment. We will aim to support your connectivity to provide a comfortable working environment whilst you oversee product testing.
Whilst your product is undergoing the testing process, take advantage of our dedicated client offices, break-out area, Wi-Fi and conferencing facilities. If a client representative cannot travel to our facility, they can remotely log onto our IT system to stream live test data and video footage of their component being tested.
Working to a tight timescale? We can conduct 24 hour testing at our facility, subject to availability. Clients also have the option to complete testing in multiple chambers.
Our largest chamber, hyperbaric chamber TPT 5, is equipped with automated controls and an interactive system to improve efficiency and reduce loading times meaning this chamber can fill, load and pressurise in just 90 minutes!
As standard, our clients receive full documentation and product certification after the testing is completed.
The majority of our hyperbaric chambers are fitted with subsea cameras and this video footage can be shared upon request.
We can offer additional services to help fulfil project requirements such as; assembly, data reporting, third party verification, logistics and storage and dedicated client facilities.
We can arrange for a third party witness to oversee your product testing and verification. We frequently work with leading authorities such as Bureau Veritas and Lloyd’s Register.
Tyne Pressure Testing performed hyperbaric ingress testing on a set of harnesses designed for a subsea environment within the oil and gas industry.
Read case study