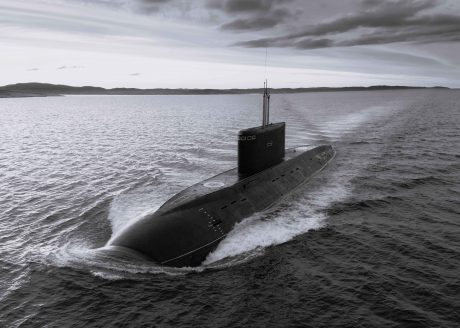
Tyne Pressure Testing partnered with a defence industry manufacturer to carry out leak testing of electronics enclosures installed on a manned underwater craft.
Read case studyCall us on +44 (0) 191 209 7490 to speak to one of our experts.
We have the capability to carry out submerged gas testing as required in API 6A.
Also known as leak testing, we can conduct high pressure gas testing using either nitrogen or heliumĀ gas. This type of testing is typically conducted in our testing bays measuring up to 6 metres long.
Gas pressure testing is performed by filling a component with nitrogen and pressurising it to test its integrity. Appropriate connections are required to connect the pressure inlet of the product to the on-site instrumentation comprising pumps, regulators, accumulators, valves and pipework. This system is then used to increase the nitrogen pressure until the desired specification is reached. Calibrated pressure transducers are used to monitor the internal pressure as it rises. The pressure is taken up and held, if the pressure drops, this indicates that there is a leakage.
Your safety, and the safety of our employees, is our main priority. Therefore all equipment which is gas tested can be observed remotely from our control room using cameras and data loggers. All testing and equipment is conducted in accordance with internationally recognisedĀ health, safety and quality standards.
Our team of highly skilled test engineers are experienced in completing gas pressure testing for a range of clients. Clients have the opportunity to select our beginning to end, fully project managed testing service or can independently hire the chambers.
If gas testing is something you require, speak to a member of our team.
Our facility offers nine hyperbaric testing chambers ranging in size and pressure capability including the worldās largest, commercially available hyperbaric chamber which can simulate water depths down to 4,500 metres.
Explore the chambersGas testing is performed by filling a component with nitrogen and pressurising it to test its integrity. Appropriate connections are required to connect the pressure inlet of the product to the on-site instrumentation comprising pumps, regulators, accumulators, valves and pipework.
This system is then used to increase the nitrogen pressure until the desired specification is reached. Calibrated pressure transducers are used to monitor the internal pressure as it rises. The pressure is taken up and held. If the pressure drops, this indicates that there is a leakage.
Gas testing is generally known as non-destructive testing and it is very rare that the product is destroyed, but it can happen.
Gas testing is used to prove that a product is fit for purpose and that it can retain its working pressure without any leaks. Therefore the worst case is generally that we will see a leak path, rather than the product being completely destroyed.
Opt for either an all-encompassing, fully project managed testing service provided by our experts and in-house engineering team, or, hire our pressure testing facilities to conduct independent testing.
Our clients travel across the globe to utilise our pressure testing services and hyperbaric testing equipment. We will aim to support your connectivity to provide a comfortable working environment whilst you oversee product testing.
Whilst your product is undergoing the testing process, take advantage of our dedicated client offices, break-out area, Wi-Fi and conferencing facilities.Ā If a client representative cannot travel to our facility, they can remotely log onto our IT system to stream live test data and video footage of their component being tested.
Working to a tight timescale? We can conduct 24 hour testing at our facility, subject to availability. Clients also have the option to complete testing in multiple chambers.
Our largest chamber, hyperbaric chamber TPT 5, is equipped with automated controls and an interactive system to improve efficiency and reduce loading times meaning this chamber can fill, load and pressurise in just 90 minutes!
As standard, our clients receive full documentation and product certification after the testing is completed.
The majority of our hyperbaric chambers are fitted with subsea cameras and this video footage can be shared upon request.
We can offer additional services to help fulfil project requirements such as; assembly, data reporting, third party verification, logistics and storage and dedicated client facilities.
We can arrange for a third party witness to oversee your product testing and verification. We frequently work with leading authorities such asĀ Bureau VeritasĀ andĀ Lloydās Register.
Tyne Pressure Testing partnered with a defence industry manufacturer to carry out leak testing of electronics enclosures installed on a manned underwater craft.
Read case study