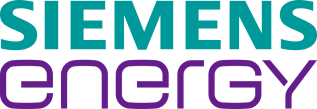
Tyne Pressure Testing performed hyperbaric ingress testing on a set of harnesses designed for a subsea environment within the oil and gas industry.
Read case studyCall us on +44 (0) 191 209 7490 to speak to one of our experts.
The assembly area covers a range of services including, mechanical, hydraulic and pneumatic equipment, integrated electrical components as well as shrink and freeze fitting.
Tyne Pressure Testing has extensive experience in product assemblies for the oil and gas, defence and civil nuclear sectors. Additional project management services include machining, testing and commissioning.
Clients using the assembly area also have access to our testing facility covering hydrostatic, hyperbaric, gas testing, temperature testing and more.
Our team of highly skilled test engineers are experienced in working with clients in the assembly area to fulfil their project requirements. Clients have the opportunity to work on-site during an assembly project in our client break out rooms, or can have their project managed by a skilled engineer.
Performance of post-assembly functional, integration and factory acceptance testing (FAT) can be offered as well as more complex forms of pressure testing including conventional hydrostatic and gas, high/low temperature environmental and ultra-deep water hyperbaric testing.
If you are interested in using the assembly area, speak to a member of our team.
Our facility offers nine hyperbaric testing chambers ranging in size and pressure capability including the world’s largest, commercially available hyperbaric chamber which can simulate water depths down to 4,500 metres.
Explore the chambersOpt for either an all-encompassing, fully project managed testing service provided by our experts and in-house engineering team, or, hire our pressure testing facilities to conduct independent testing.
Our clients travel across the globe to utilise our pressure testing services and hyperbaric testing equipment. We will aim to support your connectivity to provide a comfortable working environment whilst you oversee product testing.
Whilst your product is undergoing the testing process, take advantage of our dedicated client offices, break-out area, Wi-Fi and conferencing facilities. If a client representative cannot travel to our facility, they can remotely log onto our IT system to stream live test data and video footage of their component being tested.
Working to a tight timescale? We can conduct 24 hour testing at our facility, subject to availability. Clients also have the option to complete testing in multiple chambers.
Our largest chamber, hyperbaric chamber TPT 5, is equipped with automated controls and an interactive system to improve efficiency and reduce loading times meaning this chamber can fill, load and pressurise in just 90 minutes!
As standard, our clients receive full documentation and product certification after the testing is completed.
The majority of our hyperbaric chambers are fitted with subsea cameras and this video footage can be shared upon request.
We can offer additional services to help fulfil project requirements such as; assembly, data reporting, third party verification, logistics and storage and dedicated client facilities.
We can arrange for a third party witness to oversee your product testing and verification. We frequently work with leading authorities such as Bureau Veritas and Lloyd’s Register.
Tyne Pressure Testing performed hyperbaric ingress testing on a set of harnesses designed for a subsea environment within the oil and gas industry.
Read case study