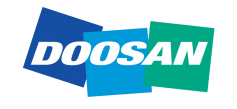
Tyne Pressure Testing has provided on-going, on-site hydrostatic testing and leak testing on fabricated stand pipes for Doosan Babcock.
Read case studyCall us on +44 (0) 191 209 7490 to speak to one of our experts.
Hydrostatic testing is a common method employed for testing subsea and topside products within the oil and gas industry and regularly carried out as part of wider factory acceptance testing (FAT).
A hydrostatic test is most commonly used to assess the strength of pressure vessels such as gas cylinders, boilers, fuel tanks and pipelines. This type of testing not only identifies leaks and manufacturing flaws, but is used to validate proof of operational capability at pressure as well as validating factors of safety required by design standards to mitigate failure in service.
Hydrostatic testing is essential to ensure the safety of a component and verify its strength and stability when operating under pressure. The vessel or pipe system is filled with liquid, usually water because of its incompressibility, and pressurised to a specific test pressure for a predetermined period of time.
A components pressure integrity is checked by pressurising it to its designated design pressure, isolating the component from the pressure source and measuring pressure loss through calibrated transducers. The component may require a visual inspection whilst at pressure to check for signs of leakage, followed by a post-test inspection to identify any issues or damage. Specific measurements and quality checks may also be carried out at this stage if required.
The pressure applied in hydrostatic testing is governed by the appropriate design standard. A factor of safety is usually added to the design pressure. A typical safety margin of 10% to 50% is added to the design pressure depending on the type of test being undertaken.
Our team of highly skilled test engineers are experienced in completing hydrostatic testing for a range of clients. Clients have the opportunity to select our beginning to end, fully project managed testing service or can independently hire the test bays.
If hydrostatic testing is something that you are interested in pleaseĀ contactĀ one of our experts to discuss your requirements.
Our facility offers nine hyperbaric testing chambers ranging in size and pressure capability including the worldās largest, commercially available hyperbaric chamber which can simulate water depths down to 4,500 metres.
Explore the chambersHydrostatic testing is performed by filling a component with water and pressurising it to test its integrity. Appropriate connections are required to connect the pressure inlet of the product to the on-site instrumentation comprising pumps, regulators, accumulators, valves and pipework. This system is then used to increase the water pressure until the desired specification is reached. Calibrated pressure transducers are used to monitor the internal pressure as it rises. The pressure is taken up and held. If the pressure drops, this indicates that there is a leakage.
If there is a requirement to monitor visible leakage, submerged gas testing can be used as an alternative to hydrostatic testing as leak paths are identified through the presence of bubbles. Submerged gas testing can also be performed at Tyne Pressure Testing.
This method of testing is generally known as non-destructive testing and it is very rare that the product is destroyed, but it can happen.
Hydrostatic testing is used to prove that a product is fit for purpose and that it can retain its working pressure without any leaks. Therefore the worst case is generally that we will see a leak path, rather than the product being completely destroyed.
Hydrostatic testing costs can vary depending on the size of the component and how comprehensive the test schedule is. The price is usually calculated based on an hourly rate and a lump sum quotation can be provided during the product development stage to help with budget forecasts.
We recommend that you contact us early in the project for a quotation.
Hydrostatic testing is mostly used to test that a prototype or new design tweak is functional and leak free. It is also common for this testing to be carried out on a production batch sample test or if the standard dictates every production unit. Testing can be carried out on existing components in the field and this is dictated by the maintenance schedule of an application normally by the end user.
Opt for either an all-encompassing, fully project managed testing service provided by our experts and in-house engineering team, or, hire our pressure testing facilities to conduct independent testing.
Our clients travel across the globe to utilise our pressure testing services and hyperbaric testing equipment. We will aim to support your connectivity to provide a comfortable working environment whilst you oversee product testing.
Whilst your product is undergoing the testing process, take advantage of our dedicated client offices, break-out area, Wi-Fi and conferencing facilities.Ā If a client representative cannot travel to our facility, they can remotely log onto our IT system to stream live test data and video footage of their component being tested.
Working to a tight timescale? We can conduct 24 hour testing at our facility, subject to availability. Clients also have the option to complete testing in multiple chambers.
Our largest chamber, hyperbaric chamber TPT 5, is equipped with automated controls and an interactive system to improve efficiency and reduce loading times meaning this chamber can fill, load and pressurise in just 90 minutes!
As standard, our clients receive full documentation and product certification after the testing is completed.
The majority of our hyperbaric chambers are fitted with subsea cameras and this video footage can be shared upon request.
We can offer additional services to help fulfil project requirements such as; assembly, data reporting, third party verification, logistics and storage and dedicated client facilities.
We can arrange for a third party witness to oversee your product testing and verification. We frequently work with leading authorities such asĀ Bureau VeritasĀ andĀ Lloydās Register.
Tyne Pressure Testing has provided on-going, on-site hydrostatic testing and leak testing on fabricated stand pipes for Doosan Babcock.
Read case study